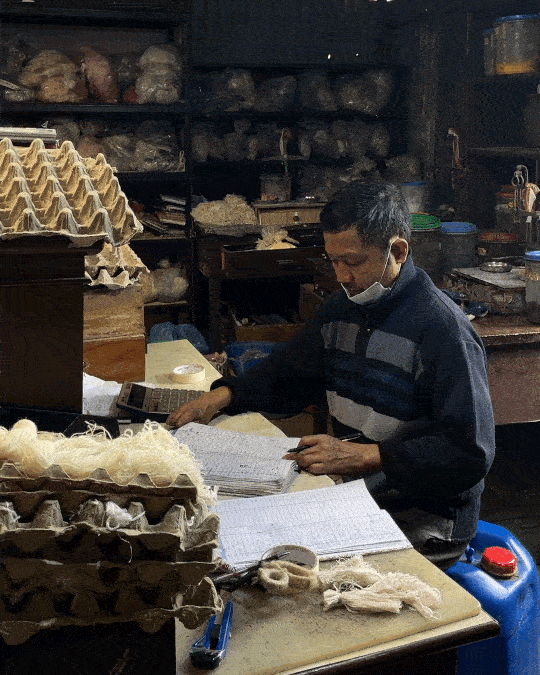
The Dye Master
Ever wondered how those stunning rug colours come to life?
Who is the Dye Master?
At every dye plantation, there's one person who holds the title of Dye Master. They’re the key figure responsible for the delicate and precise task of colouring yarn for rugs. It takes years of training and immense patience to earn this title. Through trial and error, Dye Masters develop a deep understanding of how to balance pigments for accurate colour matching and the ability to replicate them consistently.
Over the years, each Dye Master builds their own personal "recipe book," a comprehensive guide to creating specific colours. These books include detailed measurements, materials, and other critical factors like water temperature, all meticulously recorded.
Every Dye Master approaches colour differently, some techniques are learned, while others are passed down from older generations. That individuality means recipes for the same colour can vary significantly between masters, with different combinations of pigments being used to achieve identical results.
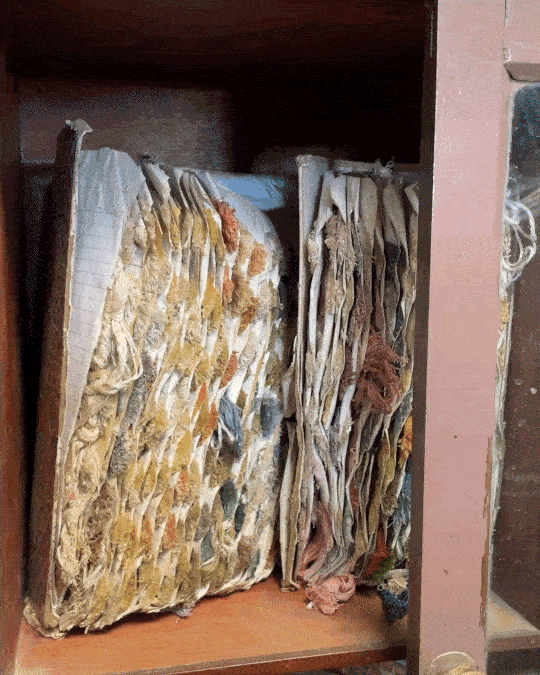
A Brief History of Dye Techniques
Historically, natural dyes made from vegetables and plants were used to color materials like wool and silk. The discovery of the first synthetic dye in 1856, created from aniline found in coal tar, marked a major turning point. This experimentation brought the color purple into the world of synthetic dyes and paved the way for the future of dyeing.
By 1870, AZO dyes had hit the market and became widely adopted by the textile industry. These synthetic dyes offer vibrant colors and are easier to produce than natural dyes. While natural dyes often require mixing multiple tones - for example, yellow and purple to make green, AZO dyes deliver singular hues. This difference means AZO dyes lack the depth and organic feel of natural dyes, but they’ve become a mainstay due to their vibrancy and consistency.
The Dye Master still adds artistry to modern techniques, creating beautiful textured effects with methods like abrash and space dyeing:
- Abrash is similar to tie-dyeing; parts of the yarn are carefully tied off to prevent the dye from fully penetrating, resulting in a unique, randomized pattern.
Space dyeing involves submerging only parts of the yarn into the dye, creating a soft, dip-dye gradient effect that adds a distinctive look to rugs.
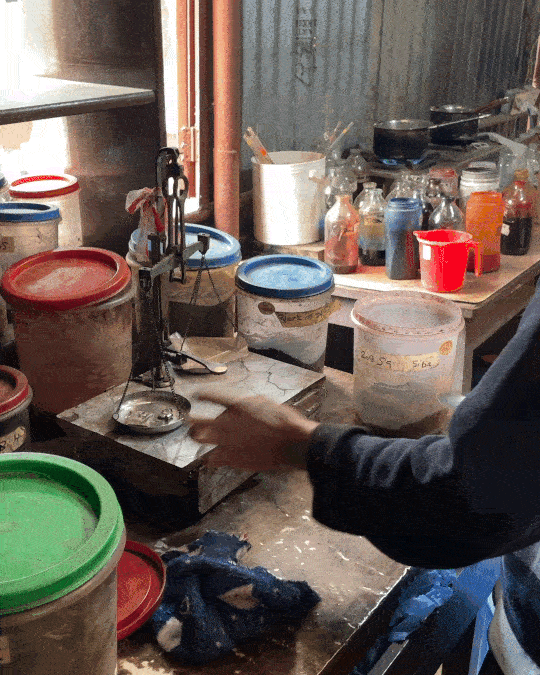
The Dye Process
Creating the perfect hue isn’t just about mixing colors—it’s a meticulous process. Here’s how it works:
1. Mixing
The Dye Master begins by weighing the dye. Precision is key, with specific measurements often including several blended colors based on their carefully curated recipe book.
2. Scouring
To prepare the wool for dyeing, it’s scoured—soaked in warm, soapy water and stirred gently for about 45 minutes. This cleanses the fibers, ensuring the dye adheres evenly. The wool is then rinsed thoroughly and left to dry.
3. Testing
Before committing to dyeing an entire batch, the Dye Master conducts a test. Using just 10 grams of yarn, they test the color to ensure it’s a perfect match to what’s needed. These small samples, along with the recipe and any notes, are always entered into the recipe book for future reference.
From careful preparation to creative artistry, the Dye Master’s work ensures vibrant, beautiful yarns that hold both character and quality.
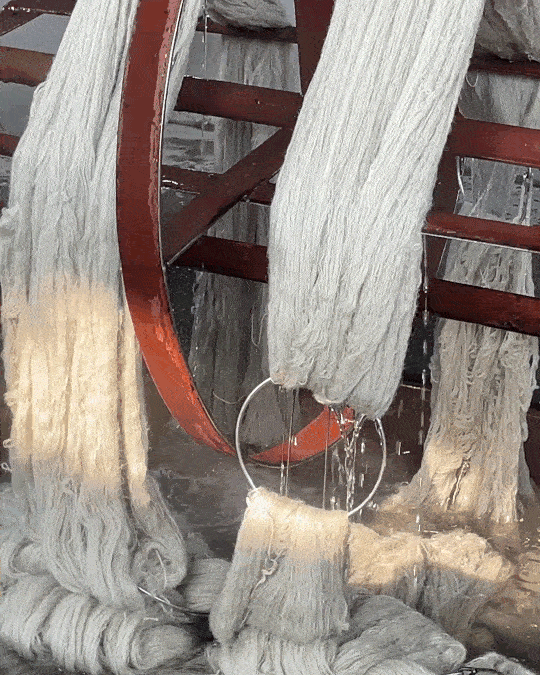
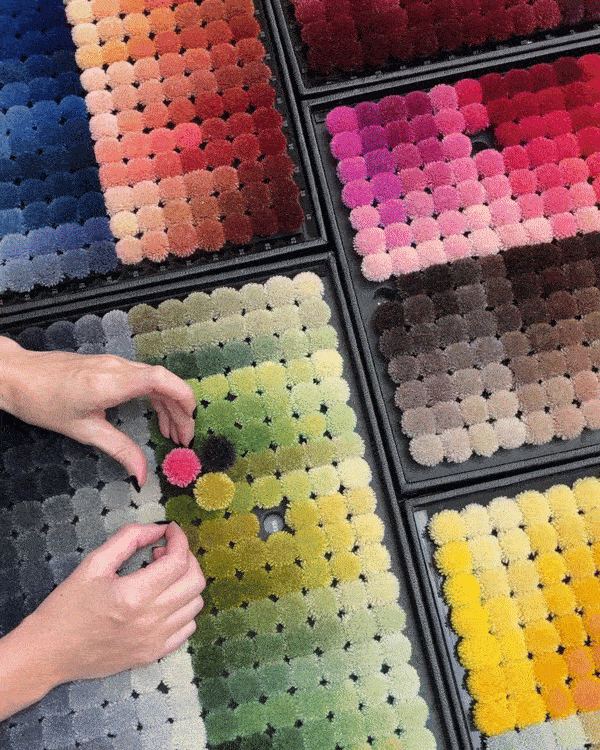
Colour Customisation
If you are looking for the perfect match for your space or style, we also offer customisation on most of our designer rugs, enabling you to achieve the exact look you are aiming for.
Coloured by the dye master
Coloured by the dye master
Emily Forgot
Amity in Pink Multi
18.01 LONDON
Carve Citrine
Eley Kishimoto
Graphic Fairytale Circular
Henry Holland
I Feel Love Red
Carmellia Indrawati
Marmalade in Lime
2LG Studio
Pill in Mottled Multicolour
Gill Thorpe