Hand Knotted
Perfect for intricate patterns as well as a dense pile underfoot, a hand knotted rug really is the finest when it comes to rug-making. Our hand knotted styles range in density from 60-knots per inch right up to 150-knots for a velvet-like softness.
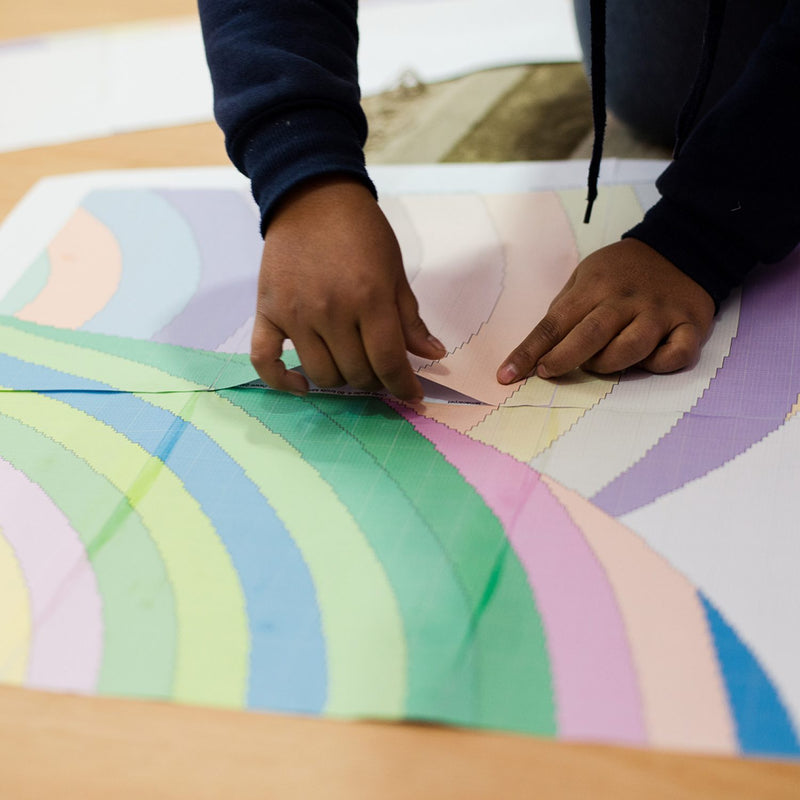
SPEC SHEET AND GRAPH DESIGN PROCESS
Once we have finalised the design between our designer and the client through a digital render (what we call a spec sheet), it is then sent off to the producer we work with in Nepal. The design will be assessed to ensure a quality outcome and once any amends have been agreed the rug will then be sent into production. The first step of this is creating a 3D model of the rug in order to translate the design into a graph for the weavers to follow row by row.
The graph is printed out lifesize and looks like a pixelated version of the design, each colour is coded in numbers. The graph also helps to break down the percentage of different colours and materials and acts as a guide for the quantity of materials that is needed to be sourced and dyed.
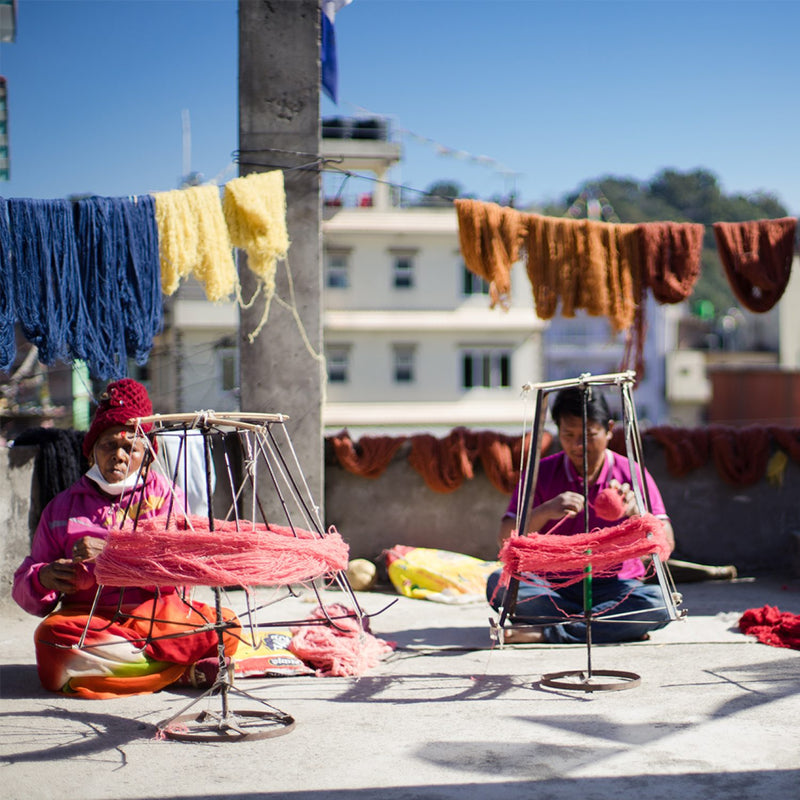
DYING AND SPINNING OF MATERIALS
The raw materials are then sent to the Dye Master and their team, who will at first test small batches to match the colours of the poms we have selected in London. Using a recipe book, built over years of practice the dye master assesses the balance of colour taking into consideration factors such as temperature to make the perfect match.
After the materials have been dyed, washed and dried, the hanks of material are then spun into balls. These balls are then colour coded before being sent to the loom so the weaver can match the correct colours to the graph.
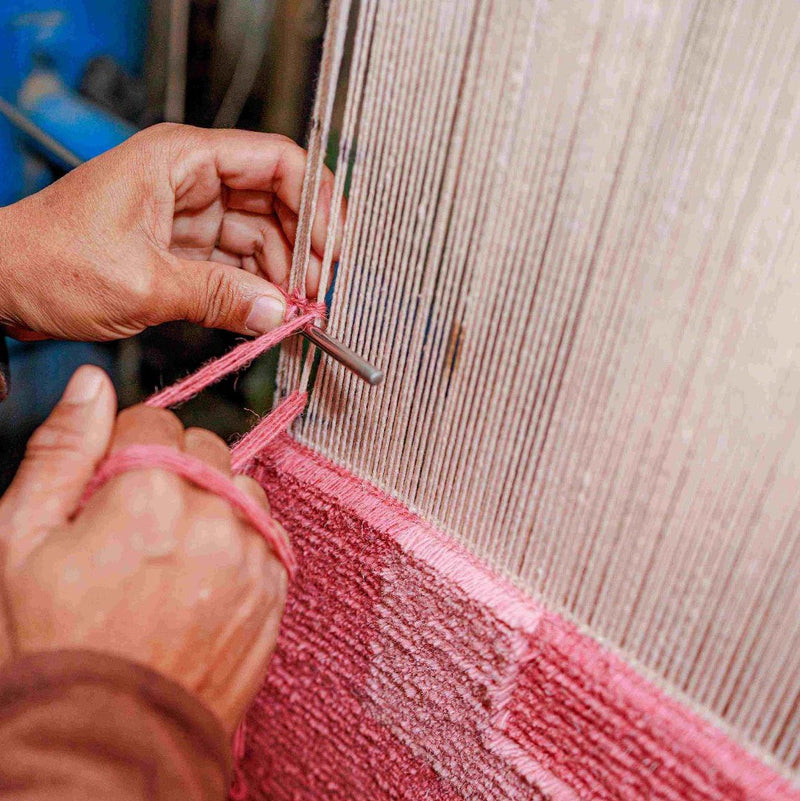
WEAVING AND OFF LOOM
The weaver will select a rod to knot the yarns with, the thickness of which determines the pile height. Wrapping the wool around cotton warp yarns and knotting it continuously in rows is what creates the body of the hand knot rug. It can take up to sixteen weeks to finish weaving a knotted rug, depending on the density and detail of the design.
The rug is then taken off the loom by cutting the warp yarns and then enters into the cleaning and finishing phase of the process. The rug is carved by hand where the weaver uses scissors or a razor to accentuate the design. The effect of the carving can be subtle or deep as well as contrasting effects like alternating pile heights.
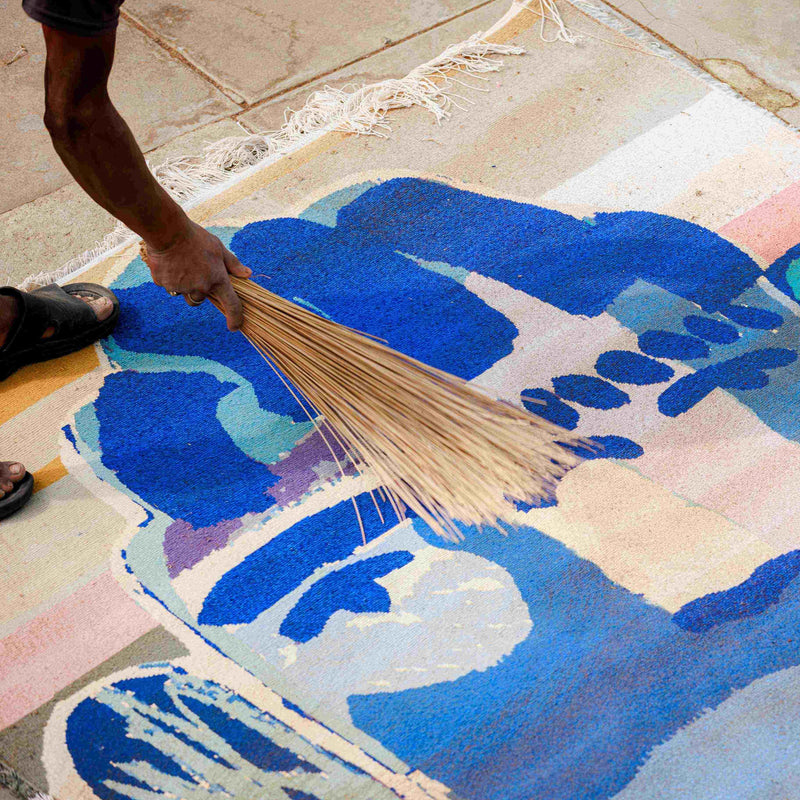
BURNING, SWEEPING, WASHING, DRYING AND STRETCHING
There are many processes alongside the weaving to ensure a high quality finish to the piece. Firstly, the rug is burned on the back to clean away any loose fibres and swept. This does not damage the rug in any way as the materials we use are naturally fire retardant.
Other elements like water are used to wash before the rug is then stretched out onto a metal frame using hooks to dry. The frame helps the rug regain its structure through stretching after the many processes it has gone through.
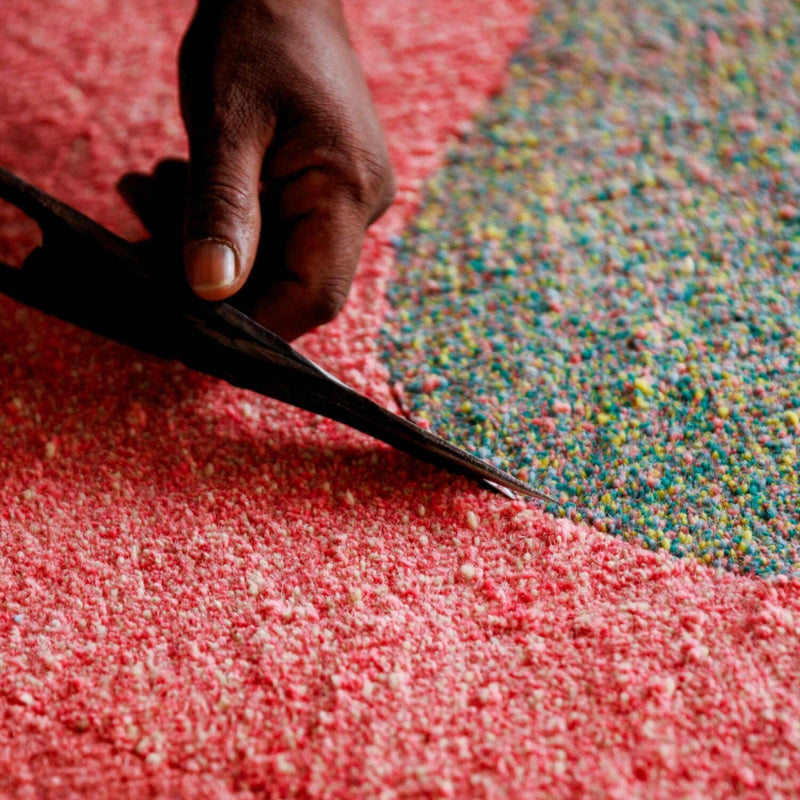
FINAL FINISHING STAGES
When the rug is completely dry it is brought back to our own facilities to go through any carving touch-ups as well as binding the outer edge of the rug. After a final quality check, the rug is then packaged and shipped either directly to the customer or to our East London showroom.
Unrolling a textile of this size and quality is a breathtaking experience, it’s the many processes and attention-to-detail from skilled weavers that sets this rug quality apart from others.
Browse our distinct hand knotted range below:
Featured
Rugs
Emily Forgot
Aldo Pink Multi
Eley Kishimoto
Graphic Fairytale Circular
Eley Kishimoto
Graphic Fairytale Circular Mono
Kangan Arora
Harlequin Runner
Henry Holland
I Feel Love Orange
Henry Holland
I Feel Love Tan
FLOOR_STORY
Leopard in Dmitri
Carmellia Indrawati
Marmalade in Lime
Carmellia Indrawati
Marmalade in Berry
Carmellia Indrawati
Marmalade in Pink Runner
2LG Studio
Pill in Mottled Multicolour
2LG Studio